Additive Manufacturing materials laboratory
The additive manufacturing is rapidly changing the production and design of the components used by the industry. This is a technology capable of creating discontinuity in the production and design of components.
The feasibility of complex geometries, the lightening of the components, the use of particular and specific chemical compositions also for small productions, the topological optimization of the distribution of the material, the availability of spare parts in a short time ... are just some of the opportunities opened by additive manufacturing.
What kind of support does the laboratory provide for this technology?
There are different areas in which the laboratory analyses are involved both in the development phase and for the production quality control.
The chemical composition of the metal powder and the controls on the degradation of the composition during the subsequent re-use of the powder cycle after cycle are an example. For instance, the phenomena of increasing of the content of N (nitrogen) and O (oxygen) in titanium alloys due to the several re-uses of the production powder are known. The control through the inert gas fusion technique (ASTM E1019) allows the determination of the content of N and O and the prevention from the re-use of powders that have exceeded the acceptability limits.
The physical characteristics of the powders such as granulometry (ASTM B214), flowability (ASTM B213) and apparent density (ASTM B212) are also subject to variations during repeated use of the powders. The analyses of these parameters are carried out in the laboratory, in accordance with the cited standards.
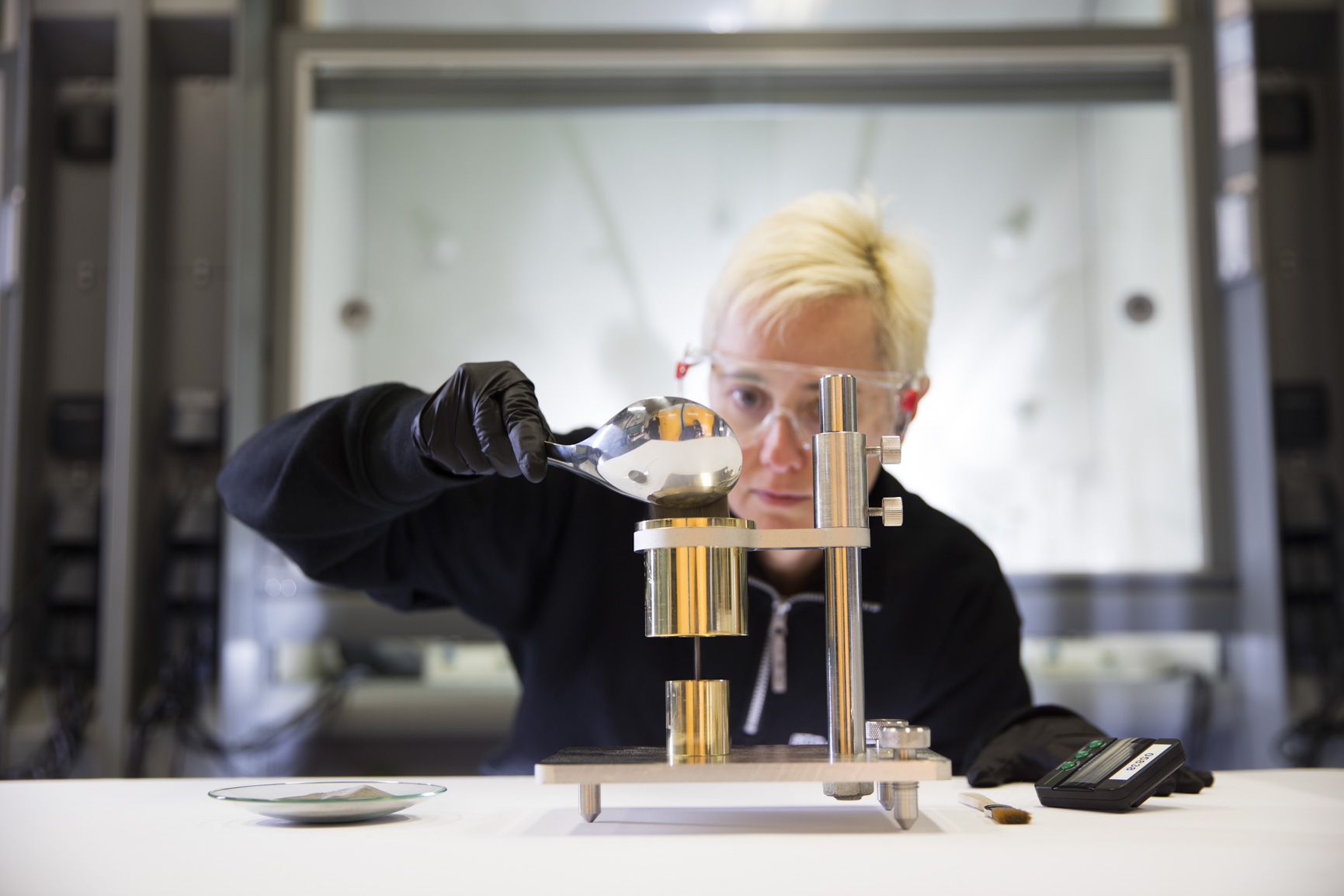
The metallographic examinations can highlight the structure at a microscopic level of the material and eventually identify detrimental or undesired phases (eg Alpha case in Titanium alloys) or detect and measure the presence of porosity. Compliance with the project specifications can be demonstrated with the analysis of sacrificial samples taken from the same production batch of the components produced.
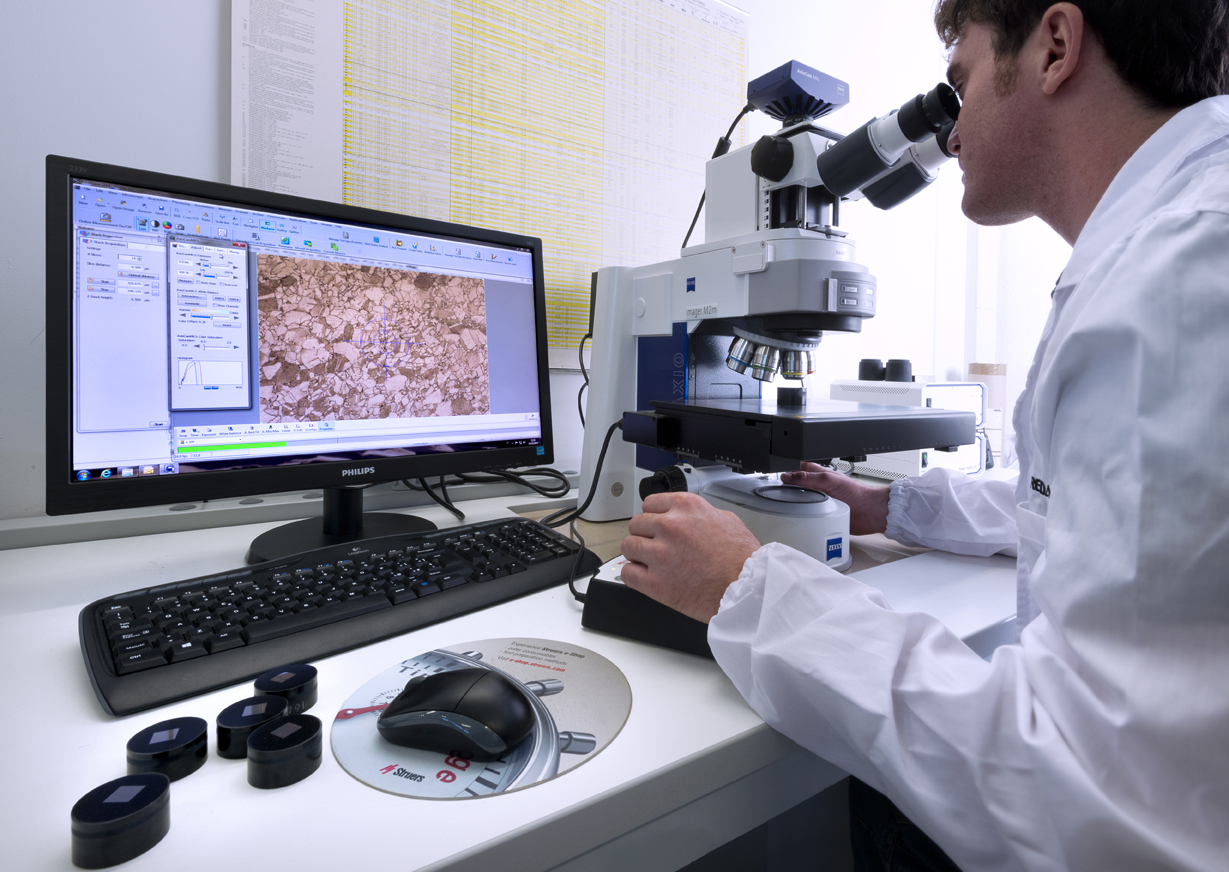
The additive generation process involves both an inhomogeneous temperature distribution, a condition suitable for generating residual tensions, and the creation of "supports" which will be subsequently removed by altering the overall equilibrium of the component. Therefore, the need to proceed with the measurement of residual stresses arises. This can be performed either with non-destructive methods using X-ray diffraction technology, or with minimally invasive methods using strain gauges rosettes and the "hole drilling" method.
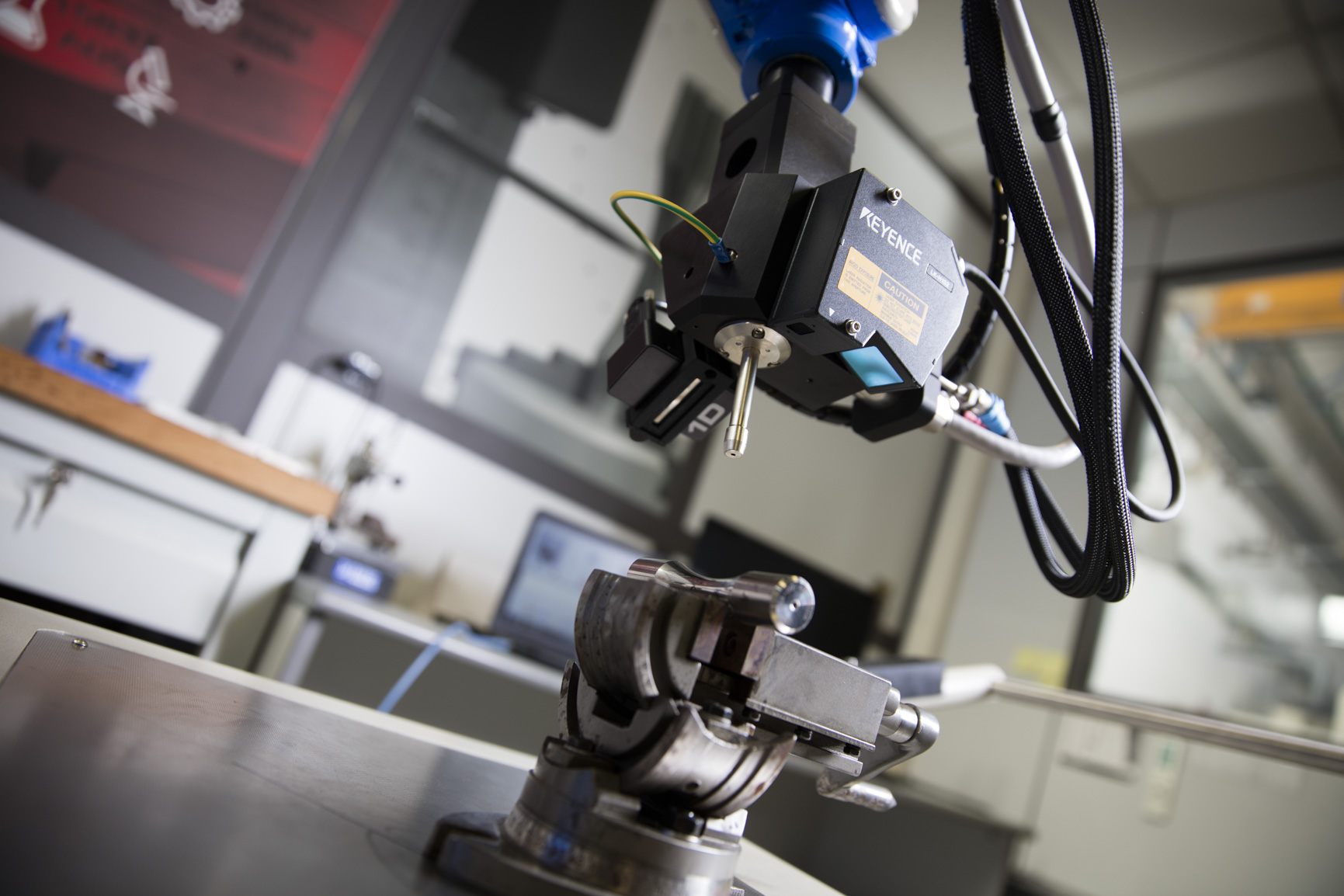
Finally, the mechanical resistance to fatigue stresses is the greatest challenge for additive production materials. The possible presence of microporosity and the surface conditions (in the as-built conditions) deriving directly from the additive production process, generate phenomena that alter the resistance to fatigue or creep of the materials, compared to products obtained through the traditional production methods and subtractive machining.
For this reason the materials are subjected to static and dynamic resistance characterizations.
Axial or rotary bending HCF (High Cycle Fatigue) tests stress the materials for long periods and for many millions of cycles, at operating temperatures (ASTM E466). Furthermore, low-cycle fatigue resistance tests (LCF) are performed in deformation control (ASTM E606) at room temperature or at operating temperature. In this case a lower number of cycles corresponds to a greater mechanical stress; the cycles can foresee sinusoidal or triangular load waves; alternatively, trapezoidal waveforms at high temperature will effectively simulate the combined effects of fatigue and creep on the material.
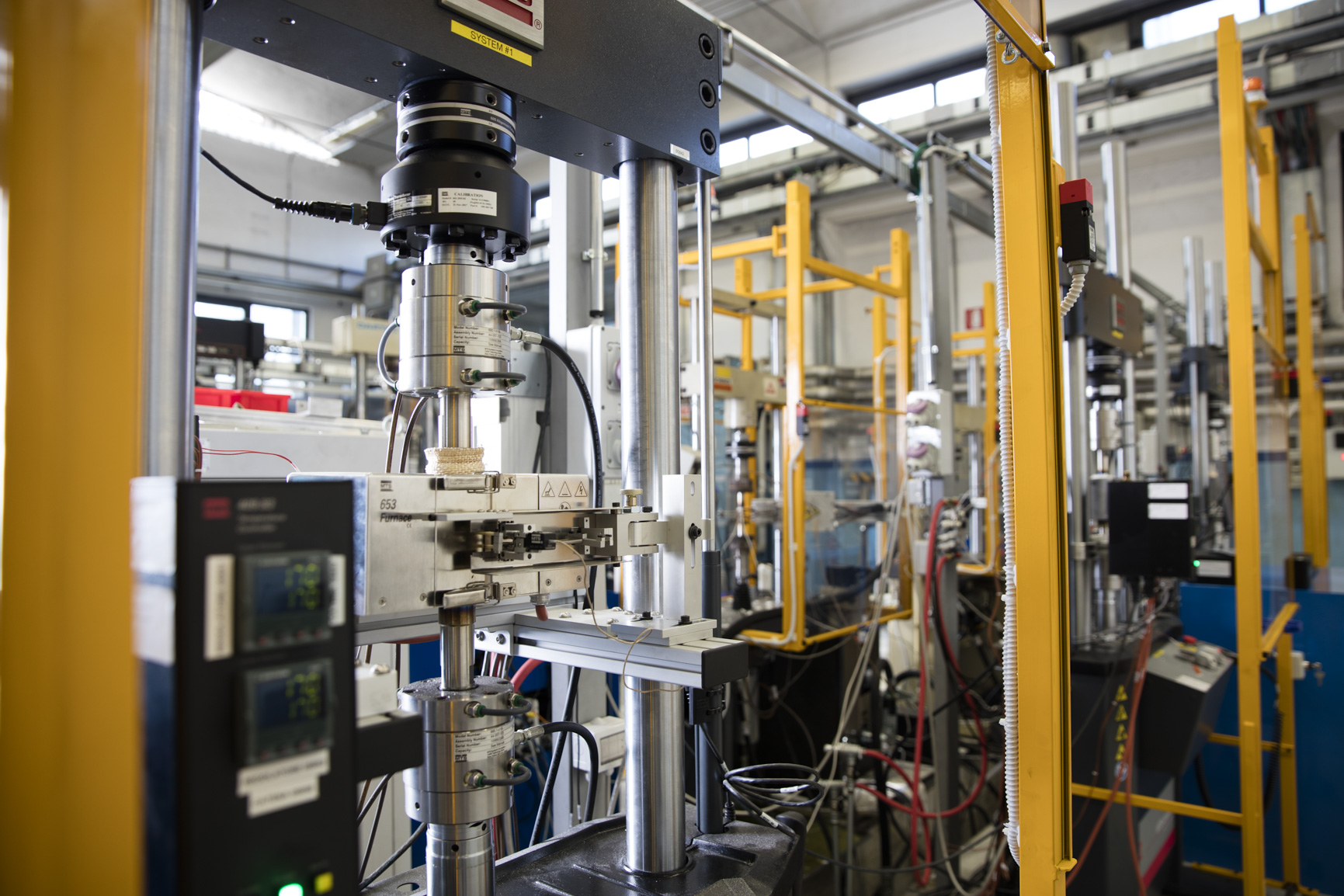
Static fracture mechanics tests or Fatigue Crack Growth Rate tests (ASTM E647) to measure the advancement speed of a crack under controlled deformation conditions are also performed in the laboratory.
A summary of the recommended mechanical tests for materials produced with additive technology is provided in ASTM F3122 (Standard guide for evaluating mechanical properties of metal materials made via additive manufacturing processes).